

-
Electronic Products Finding & Locating
-
Hard to Find Electronics
-
Domestic & Global Electronics Procurement
-
Electronics Prototyping
-
Custom Manufacturing
-
Domestic & Global Contract Manufacturing
-
Manufacturing Outsourcing
-
Electronics Assembly
-
Consolidation
-
Engineering Integration
Electronics Global Supplier, Prototyping House, Mass Producer, Custom Manufacturer, Engineering Integrator, Consolidator, Outsourcing and Contract Manufacturing Partner.
We are your one-stop source for electronic components, prototypes, sub-assemblies, assemblies, finished products and supplies.
Choose your LANGUAGE

Computer Integrated Manufacturing at AGS-Electronics
Our COMPUTER INTEGRATED MANUFACTURING (CIM) SYSTEMS interlink the functions of product design, research and development, production, assembly, inspection, quality control and others. AGS-Electronics's computer integrated manufacturing activities include:
- COMPUTER-AIDED DESIGN (CAD) and ENGINEERING (CAE)
- COMPUTER-AIDED MANUFACTURING (CAM)
- COMPUTER-AIDED PROCESS PLANNING (CAPP)
- COMPUTER SIMULATION of MANUFACTURING PROCESSES and SYSTEMS
- GROUP TECHNOLOGY
- CELLULAR MANUFACTURING
- FLEXIBLE MANUFACTURING SYSTEMS (FMS)
- HOLONIC MANUFACTURING
- JUST-IN-TIME PRODUCTION (JIT)
- LEAN MANUFACTURING
- EFFICIENT COMMUNICATION NETWORKS
- ARTIFICIAL INTELLIGENCE SYSTEMS
COMPUTER-AIDED DESIGN (CAD) and ENGINEERING (CAE): We use computers to create design drawings and geometric models of products. Our powerful software like CATIA enables us to conduct engineering analysis to identify potential problems such as interference at mating surfaces during assembly. Other information such as materials, specifications, manufacturing instructions…etc. are also stored in the CAD database. Our customers can submit us their CAD drawings in any of the popular formats used in the industry, such as DFX, STL, IGES, STEP, PDES. Computer-Aided Engineering (CAE) on the other hand simplifies the creation of our database and allows various applications to share the information in the database. These shared applications include valuable information from finite-element analysis of stresses and deflections, temperature distribution in structures, NC data to name a few. After geometric modeling, the design is subjected to engineering analysis. This may consist of tasks such as analyzing stresses and strains, vibrations, deflections, heat transfer, distribution of temperature and dimensional tolerances. We use special software for these tasks. Prior to production, we may sometimes conduct experiments and measurements to verify the actual effects of loads, temperature and other factors on the component samples. Again, we do use special software packages with animation capabilities to identify potential problems with moving components in dynamic situations. This capability makes it possible to review and evaluate our designs in an effort to precisely dimension the parts and set appropriate production tolerances. Detail and working drawings are also produced with the help of these software tools we use. The database management systems which are built into our CAD systems allow our designers to identify, view and access parts from a library of stock parts. We must emphasize that CAD and CAE are two essential elements of our computer integrated manufacturing system.
COMPUTER-AIDED MANUFACTURING (CAM): Without doubt, another essential element of our computer integrated manufacturing system is CAM which reduces cost and increases productivity. This involves all phases of manufacturing where we use computer technology and enhanced CATIA, including process and production planning, scheduling, manufacture, QC and management. Computer-aided design and computer-aided manufacturing are combined into CAD/CAM systems. This allows us to transfer information from the design stage to planning stage for the product manufacture without the need to manually reenter the data on part geometry. The database developed by CAD is further processed by CAM into the necessary data and instructions for operating and controlling production machinery, automated testing and inspection of products. CAD/CAM system allows us to display and visually check tool paths for possible tool collisions with fixtures and clamps in operations such as machining. Then, if needed, the tool path can be modified by the operator. Our CAD/CAM system is also capable of coding and classifying parts into groups that have similar shapes.
COMPUTER-AIDED PROCESS PLANNING (CAPP): Process planning involves the selection of production methods, tooling, fixturing, machinery, operations sequence, standard processing times for individual operations and assembly methods. With our CAPP system we view the total operation as an integrated system with individual operations being coordinated with each other to produce the part. In our computer integrated manufacturing system, CAPP is an essential adjunct to CAD/CAM. It is vital for efficient planning and scheduling. The process-planning capabilities of computers can be integrated into the planning and control of production systems as a subsystem of computer-integrated manufacturing. These activities enable us capacity planning, control of inventory, purchasing and production scheduling. As part of our CAPP we have computer-based ERP system for effective planning and control of all the resources needed to take orders for products, produce them, ship them to the customers, service them, do the accounting and billing. Our ERP system is not only to the benefit of our corporation, but indirectly also to the benefit of our customers.
COMPUTER SIMULATION of MANUFACTURING PROCESSES and SYSTEMS:
We use finite-element analysis (FEA) for process simulations of specific manufacturing operations as well as for multiple processes and their interactions. Process viability is routinely studied using this tool. An example is assessing the formability and behavior of sheet metal in pressworking operation, process optimization by analyzing the metal-flow pattern in forging a blank and identifying potential defects. Yet another example application of FEA would be to improve mold design in casting operation to reduce and eliminate hot spots and minimize defects by achieving uniform cooling. Entire integrated manufacturing systems are also simulated to organize plant machinery, achieve better scheduling and routing. Optimizing the sequence of operations and organization of machinery helps us effectively reduce manufacturing costs in our computer integrated production environments.
GROUP TECHNOLOGY: The group technology concept seeks to take advantage of the design and processing similarities among the parts to be produced. It is a valuable concept in our computer integrated lean manufacturing system. Many parts have similarities in their shape and method of manufacture. For example all shafts can be categorized into one family of parts. Similarly, all seals or flanges can be categorized into the same families of parts. Group technology helps us in economically manufacturing an ever-larger variety of products, each in smaller quantities as batch production. In other words, group technology is our key for inexpensive manufacturing of small quantity orders. In our cellular manufacturing, machines are arranged in an integrated efficient product flow line, named “group layout”. The manufacturing cell layout depends on the common features in parts. In our group technology system parts are identified and grouped into families by our computer controlled classification and coding system. This identification and grouping is done according to parts design and manufacturing attributes. Our advanced computer integrated decision-tree coding / hybrid coding combines both design and manufacturing attributes. Implementing group technology as part of our computer integrated manufacturing helps AGS-Electronics by:
-Making possible the standardization of part designs / minimization of design duplications. Our product designers can easily determine whether data on a similar part already exists in the computer database. New part designs can be developed using already existing similar designs, thereby saving on design costs.
-Making data from our designers and planners stored in the computer integrated database available to less experienced personnel.
-Enabling statistics on materials, processes, number of produced parts….etc. easy to be used to estimate manufacturing costs of similar parts and products.
-Allowing efficient standardization and scheduling of process plans, grouping of orders for efficient production, better machine utilization, reducing setup times, facilitating the sharing of similar tools, fixtures and machines in the production of a family of parts, increasing overall quality in our computer integrated manufacturing facilities.
-Improving productivity and reducing costs especially in small-batch production where it is needed the most.
CELLULAR MANUFACTURING: Manufacturing cells are small units consisting of one or more computer integrated workstations. A workstation contains either one or several machines, each of which performs a different operation on the part. Manufacturing cells are effective in producing families of parts for which there is a relatively constant demand. Machine tools used in our manufacturing cells are generally lathes, milling machines, drills, grinders, machining centers, EDM, injection molding machines…etc. Automation is implemented in our computer integrated manufacturing cells, with automated loading/unloading of blanks and workpieces, automated changing of tools and dies, automated transfer of tools, dies and workpieces between workstations, automated scheduling and control of operations in the manufacturing cell. In addition, automated inspection and testing takes place in the cells. Computer integrated cellular manufacturing offers us reduced work in progress and economic savings, improved productivity, ability to detect quality issues right away without delay among other benefits. We also deploy computer integrated flexible manufacturing cells with CNC machines, machining centers and industrial robots. The flexibility of our manufacturing operations offers us the advantage of adapting to rapid changes in market demand and manufacturing more product variety in smaller quantities. We are able to process very different parts quickly in sequence. Our computer integrated cells can manufacture parts in batch sizes of 1 pc at a time with negligible delay between parts. These very short delays in between are for downloading new machining instructions. We have achieved building unattended computer integrated cells (unmanned) for economically manufacturing your small orders.
FLEXIBLE MANUFACTURING SYSTEMS (FMS): Major elements of manufacturing are integrated into a highly automated system. Our FMS consist of a number of cells each containing an industrial robot that serves several CNC machines and an automated material-handling system, all interfaced with a central computer. Specific computer instructions for the manufacturing process can be downloaded for each successive part that passes through a workstation. Our computer integrated FMS systems can handle a variety of part configurations and produce them in any order. Furthermore the time required for changeover to a different part is very short and therefore we can respond very quickly to product and market-demand variations. Our computer controlled FMS systems carry out machining and assembly operations involving CNC machining, grinding, cutting, forming, powder metallurgy, forging, sheet metal forming, heat treatments, finishing, cleaning, part inspection. Material handling is controlled by central computer and carried out by automated guided vehicles, conveyors or other transfer mechanisms depending on production. Transportation of raw materials, blanks and parts in various stages of completion can be made to any machine, in any order at any time. Dynamic process planning and scheduling takes place, capable of responding to quick changes in product type. Our computer integrated dynamic scheduling system specifies the types of operations to be performed on each part and identifies the machines to be used. In our computer integrated FMS systems no setup time is wasted when switching between manufacturing operations. Different operations can be carried out in different orders and on different machines.
HOLONIC MANUFACTURING: Components in our holonic manufacturing system are independent entities while being a subservient part of a hierarchical & computer integrated organization. In other words they are part of a “Whole”. Our manufacturing holons are autonomous and cooperative building blocks of a computer integrated manufacturing system for production, storage, and transfer of objects or information. Our computer integrated holarchies can be created and dissolved dynamically, depending on the current needs of the particular manufacturing operation. Our computer integrated manufacturing environment enables maximum flexibility through providing intelligence within holons to support all production and control functions required to complete production tasks and manage the equipment and systems. The computer integrated manufacturing system reconfigures into operational hierarchies to optimally produce products with holons being added or removed as needed. AGS-Electronics factories consist of a number of resource holons available as separate entities in a resource pool. Examples are CNC milling machine and operator, CNC grinder and operator, CNC lathe and operator. When we receive a purchase order, an order holon is formed which starts to communicate and negotiate with our available resource holons. As an example, a work order may require the use of a CNC lathe, CNC grinder and an automated inspection station to organize them into a production holon. Production bottlenecks are identified and eliminated through computer integrated communication and negotiation between holons in the resource pool.
JUST-IN-TIME PRODUCTION (JIT): As an option, we do provide Just-In-Time (JIT) production to our customers. Again, this is only an option we do offer to you in case you want or need it. Computer integrated JIT eliminates waste of materials, machines, capital, manpower and inventory throughout the manufacturing system. Our computer integrated JIT production involves:
-Receiving supplies just in time to be used
-Producing parts just in time to be turned into subassemblies
-Producing subassemblies just in time to be assembled into finished products
-Production and delivery of finished products just in time to be sold
In our computer integrated JIT we produce parts to order while matching production with demand. There are no stockpiles, and no extra motions retrieving them from storage. In addition, parts are inspected in real time as they are being manufactured and are used within a short time period. This enables us to maintain control continuously and immediately to identify defective parts or process variations. Computer integrated JIT eliminates undesirable high inventory levels which can mask quality and production problems. All operations and resources that do not add value are eliminated. Our computer integrated JIT production offers our customers the option of eliminating the need to rent large warehouses and storage facilities. Computer integrated JIT results in high-quality parts and products at low cost. As part of our JIT system, we do use computer integrated KANBAN bar-coding system for production and conveyance of parts and components. On the other hand, JIT production may lead to higher production costs and higher per piece prices for our products.
LEAN MANUFACTURING: This involves our systematic approach to identifying and eliminating waste and non-value added activities in every area of manufacturing through continuous improvement, and emphasizing product flow in a pull system rather than a push system. We continuously review all our activities from the viewpoint of our customers and optimize processes to maximize added value. Our computer integrated lean manufacturing activities include elimination or minimization of inventory, minimization of waiting times, maximization of our workers efficiency, elimination of unnecessary processes, minimization of product transportation and elimination of defects.
EFFICIENT COMMUNICATION NETWORKS: For high level coordination and efficiency of operation in our computer integrated manufacturing we have an extensive, interactive high-speed communications network. We deploy LAN, WAN, WLAN and PANs for effective computer integrated communication between personnel, machines and buildings. Different networks are linked or integrated through gateways and bridges using secure file transfer protocols (FTP).
ARTIFICIAL INTELLIGENCE SYSTEMS: This relatively new area of computer science finds applications to some degree in our computer integrated manufacturing systems. We take advantage of expert systems, computer machine vision and artificial neural networks. Expert systems are used in our computer-aided design, process planning and production scheduling. In our systems incorporating machine vision, computers and software are combined with cameras and optical sensors to perform operations like inspection, identification, sorting of parts and guiding robots.
Taking automation and quality as a necessity, AGS-Electronics / AGS-TECH, Inc. has become a value added reseller of QualityLine production Technologies, Ltd., a high-tech company that has developed an Artificial Intelligence based software solution that automatically integrates with your worldwide manufacturing data and creates an advanced diagnostics analytics for you. This powerful software tool is an especially good fit for electronics industry and electronics manufacturers. This tool is really different than any others in the market, because it can be implemented very quickly and easily, and will work with any type of equipment and data, data in any format coming from your sensors, saved manufacturing data sources, test stations, manual entry .....etc. No need to change any of your existing equipment to implement this software tool. Besides real time monitoring of key performance parameters, this AI software provides you root cause analytics, provides early warnings and alerts. There is no solution like this in the market. This tool has saved manufacturers plenty of cash reducing rejects, returns, reworks, downtime and gaining customers goodwill. Easy and quick ! To schedule a Discovery Call with us and to find out more about this powerful artıficial intelligence based manufacturing analytics tool:
- Please fill out the downloadable QL Questionnaire from the blue link on the left and return to us by email to sales@agstech.net.
- Have a look at the blue colored downloadable brochure links to get an idea about this powerful tool. QualityLine One Page Summary and QualityLine Summary Brochure
- Also here is a short video that gets to the point: VIDEO of QUALITYLINE MANUFACTURING ANALYTICS TOOL
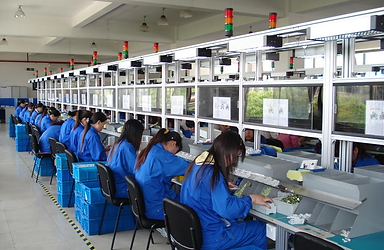
AGS-Electronics is your Global Supplier of Electronics, Prototyping House, Mass Producer, Custom Manufacturer, Engineering Integrator, Consolidator, Outsourcing and Contract Manufacturing Partner